Organic light-emitting diodes (OLEDs) have already found acceptance as a light source in first luminaires on the market on rigid glass. However, far larger shares of the market could be acquired, if flexible large-area OLEDs could be manufactured cost-effectively with consistent quality. Scientists are working feverishly on this worldwide. Large-area OLEDs could be employed not only in innovative furniture designs, but also deliver good service in other sectors requiring specialized curved design, such as architectural lighting and automotive, for example. The organic layers of the OLED are sensitive to oxygen and moisture and needs to be well protected. Flexible ultra-thin glass meets the stringent requirements of a hermetic barrier, free of defects and pinhole freedom for large OLED emissive surfaces.
Fraunhofer FEP has had success not only in applying OLEDs to flexible ultra-thin glass, but also in encapsulating the devices using an additional thin glass layer in a single roll-to-roll manufacturing step. A high-performance adhesive was applied over the entire surface of the encapsulating glass in advance in collaboration with tesa SE. This adhesive glass film is subsequently laminated to the OLED-coated ultra-thin glass. Fraunhofer FEP will be presenting this type of OLED at AIMCAL 2016, in this case based on G-Leaf™ ultra-thin glass by Nippon Electric Glass Co Ltd. (NEG). A 10 cm × 25 cm emissive surfaces will be on display.
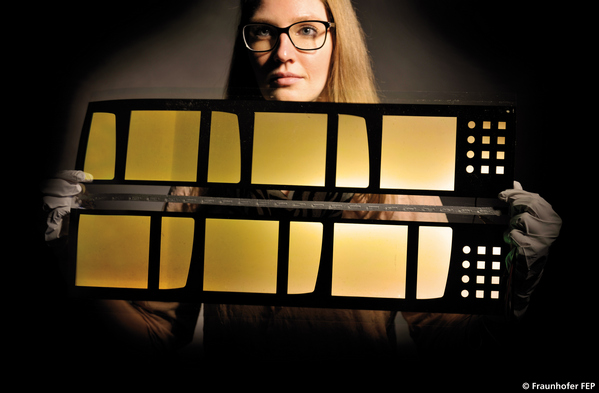 |
Fraunhofer Institute's glass-on-glass Laminated OLEDs. (Photo courtesy of Fraunhofer FEP) |
“But encapsulation is not the only challenge for flexible large area OLEDs that need to remain stable over long periods. In order to get them to emit, a highly conductive, transparent oxide layer with good light coupling properties is required and reliable electrical contacts to the emitting layers with low contact resistance is essential," explains Dr. Stefan Mogck, Head of Roll-to-Roll Organic Technology at Fraunhofer FEP. “We are proud of having optimized our process, and that these layers can be applied very homogenously to the flexible glass.”
Making dependable electrical connections to the ultra-thin glass without damaging it was especially challenging. The scientists will be working with customers in the future on non-destructive techniques of integration.
Fraunhofer FEP offers its industrial partners process and product development over the complete value chain customized to their requirements. Processes for treatment and coating flexible glass for customer-specific emissive surfaces in different sizes and colors can be developed, and even flexible OLED prototypes fabricated at customers’ requests. In addition, the Institute can develop matching driver circuitry for supplying power to the prototypes.
Fraunhofer FEP at AIMCAL 2016
Talks
Monday, May 30
Session: Coating and Laminating Short Course
13:30 – 17:00, Location: Bellevue I
Oliver Miesbauer, Fraunhofer IVV / Dr. rer. nat. John Fahlteich, Fraunhofer FEP
Tuesday, May 31
Track: Web Coating and Web Handling,
Session: Web Surface / Barrier
14:30 – 15:00, Location: Bellevue I
Surface modification of polyethylene terephthalate (PET) and oxide coated PET for adhesion improvement
Juliane Fichtner, Fraunhofer FEP
Track: Vacuum
Session: Sputtering, Coating Equipment, Inline control
16:00 – 16:30, Location: Bellevue II
Adapted particle bombardment during layer growth by pulse magnetron sputtering
Dr. rer. nat. Daniel Glöß, Fraunhofer FEP
Wednesday, June 1
Track: Vacuum
Session: Pretreatment, Substrate Film, Simulation
10:30 – 11:00, Location: Bellevue II
Vacuum plasma treatment and coating of fluoropolymer webs – challenges and applications
M.Eng. Cindy Steiner, Fraunhofer FEP
Thursday, June 2
Track: Vacuum
Session: New Applications, Emerging Technologies, Capacitors, Photovoltaic
8:30 – 9:00, Location: Bellevue II
New vacuum coating technologies for metal strips and foils
Prof. Dr. rer. nat. Christoph Metzner, Fraunhofer FEP
10:30 – 11:00, Location: Bellevue II
Present status of Roll-to-Roll Fabrication for OLED lighting
Michael Stanel, Fraunhofer FEP